トヨタ生産方式(TPS)は、トヨタ自動車が長年の実践と改善を積み重ねて確立した、徹底的なムダの排除を追求する生産方式です。単に効率的な生産を目指すだけでなく、働く人をより働きやすく、楽にすることを前提としています。
現状に満足せずに、作業の効率化、品質の安定化、作業者の負担軽減などを目的としたカイゼン(改善)活動というのも存在し、誰でも、簡単に、同じ時間で、同じ品質で作ることができるようにする、この考え方は製造業以外の様々な分野で応用させることができます。
☆こんな人におすすめ☆
・トヨタ生産方式ってなに?
・トヨタ生産方式を取り入れていきたいけど課題は?
トヨタ生産方式(TPS)の導入には課題が多い
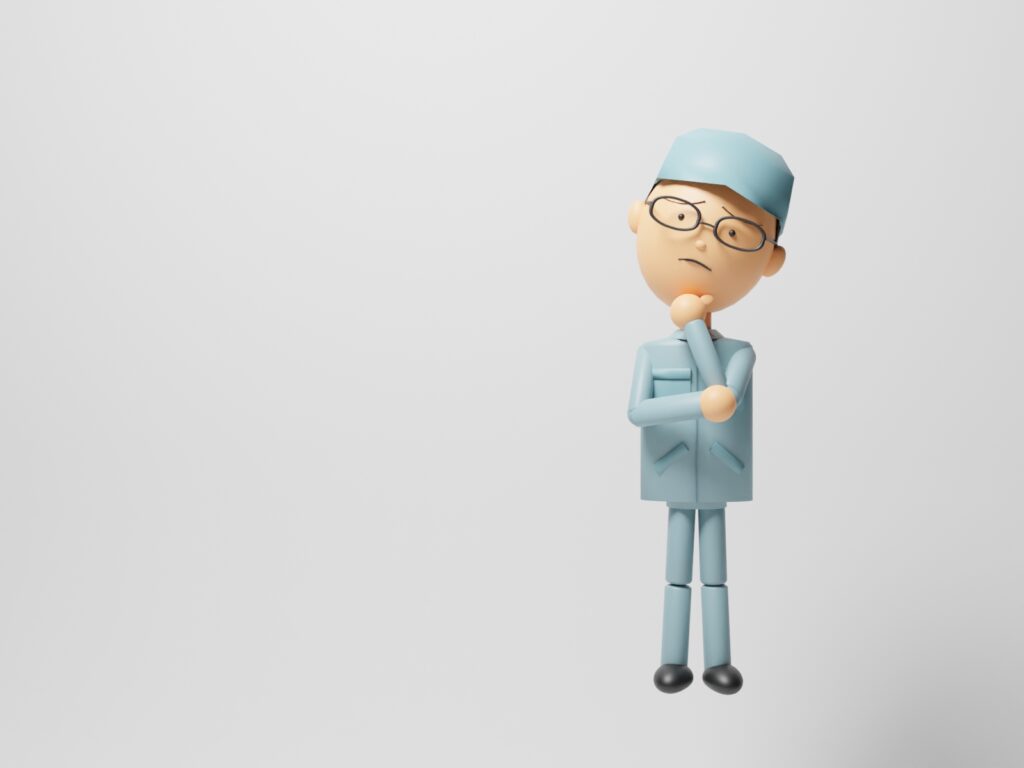
トヨタ生産方式(TPS)に関する情報は、トヨタ自動車自身や関連団体、書籍などを通じて、ある程度公開されています。トヨタ自動車の公式ウェブサイトでは 経営理念の一部としてトヨタ生産方式の基本的な考え方や要素(ジャスト・イン・タイム、自働化、ムダの排除など)が紹介されています。また、「トヨタバーチャル工場見学」では、生産工程やTPSの考え方を映像と解説で学ぶことができることによって規模の大小に関わらず、様々な中小企業にとって経営改善の有効な手段となり得ます。
トヨタ生産方式(TPS)は、その効率性と品質向上への貢献から多くの企業に参考にされていますが、一方で、働く環境や従業員の視点から見ると、必ずしも全ての人に好意的に受け止められているわけではありません。 「嫌われる」とまでは言えないかもしれませんが、批判や課題が指摘されることもあります。その理由について解説していきます。
課題1:導入する側とされる側の温度差
基本的にトヨタ生産方式(TPS)の導入を検討する企業は、業種や規模を問わずコスト削減や品質向上を目的としていることが多いかと思います。ですが「流行だから」「他社がやっているから」といった安易な動機でトヨタ生産方式( TPS)の本質を理解せず、単なるブームとして捉えて導入すると従業員にTPS導入の意義やメリットが伝わらず、抵抗感や不信感が生まれます。また、現場の状況や課題を十分に把握せず、上層部の判断だけで導入を決定し、現場に一方的に押し付けることで働く人にプレッシャーを与える可能性があります。目標達成へのプレッシャーや、常に改善を求められる状況が、精神的な負担となる場合があります。
これらの温度差を解消するためには、上司自身がTPSの本質を深く理解し、現場とのコミュニケーションを密にし、長期的な視点を持って粘り強く取り組む姿勢が重要です。また、従業員の意見を尊重し、共に学び、改善していくという意識を持つことが、TPS導入を成功に導く鍵となります。
課題2:短期的な成果を急ぎすぎる
トヨタ生産方式(TPS)を導入した企業の多くはすぐに効果が出ると期待してしまいます。TPSは組織全体の体質改善を目指すものであり、効果が出るまでに時間がかかることを理解していないと色々な改善に手を付け本来の効果を見失ってしまう事があり現場を混乱させてしまいます。また本質的な改善よりも、数字上の成果や形式的な導入にばかり目を向けてしまうことにも注意が必要です。
課題3:人間性の軽視
効率や生産性ばかりが重視され、働く人の個性や感情、体調などが考慮されにくいという批判もあります。実際に作業時間の現状分析にはストップウォッチでの計測が一般的ですが、自分の作業時間をいきなり測定されると現場の作業者は不快感を示すことが多くあります。
作業が細かく標準化されひとつひとつの動作に時間が設けられ時間当たりのノルマを与えられると『ロボットの様な扱いをされている』と認識する人もいます。
効率化の追求と人間性の尊重のバランスをどのように取るかは、TPSを導入・運用する企業にとって重要な課題です。単に効率を高めるだけでなく、働く人の意見に耳を傾け、働きがいのある環境を整備していくことが、持続的な成長には不可欠となります。
トヨタ生産方式(TPS)は目的ではなく手段
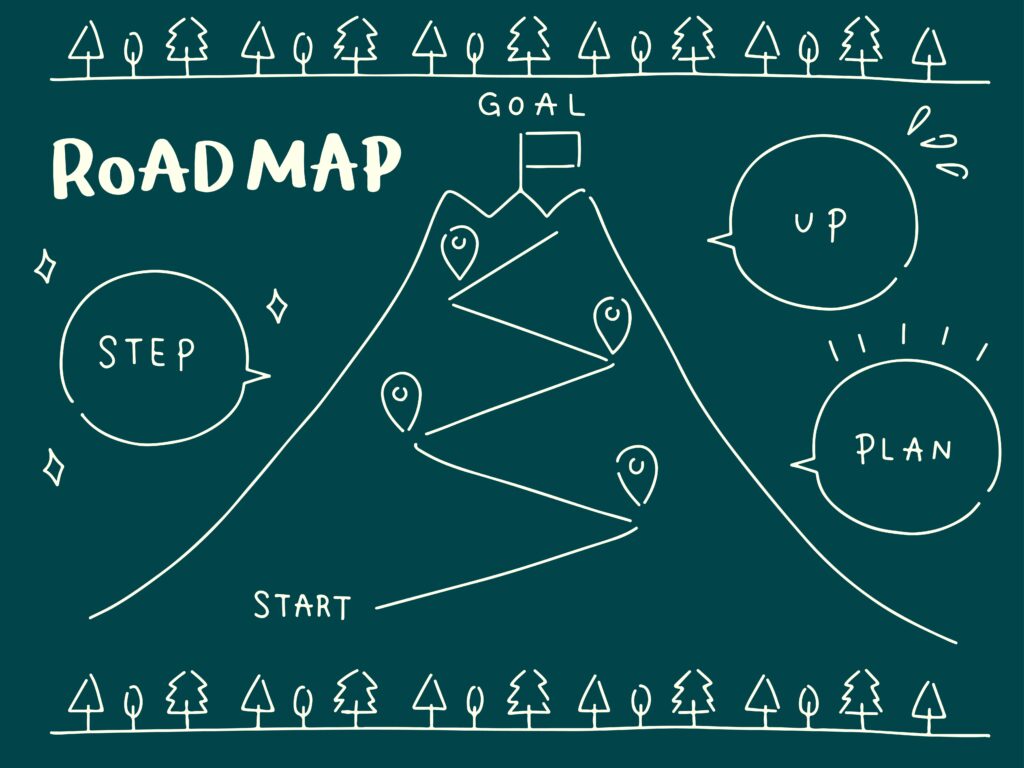
トヨタ生産方式(TPS)の導入を、本来の目的達成のための手段として捉えられずにそれ自体が目的となってしまうのは、TPS導入における非常に危険な落とし穴です。このような状態に陥ると、本質的な課題解決から遠ざかり、様々な弊害が生じる可能性があります。
なんの改善もせずにいきなり『かんばん』というツールを導入しても全く効果が無く、ただ現場に混乱を招くだけになります。登山と同じように麓から少しづつ確実に頂上を目指すのがTPS導入の成功に繋がります。
トヨタ生産方式(TPS)は、単なる個別のツールや手法の集合体ではなく、**「ムダの徹底的な排除」と「品質の作り込み」**という二つの柱を支える哲学と実践的な活動全体を指します。しかし、その考え方を具現化し、現場で機能させるための様々なツールや手法が存在します。
ここでは、TPSでよく用いられる主要なツールや手法をいくつかご紹介します。
かんばん方式
・目的: 過剰な在庫を抑制し、必要なものを必要な時に必要なだけ生産・供給する「同期化」を実現する。
・詳細:生産指示、部品の払い出し指示、運搬指示などの情報を視覚的に伝え、生産のムダ(作りすぎ、手待ち、運搬など)を最小限に抑える事ができます。
後工程引き取り
・目的: 前工程が後工程の要求に応じて生産することで、作りすぎのムダを根本的に防止する。
・詳細: 需要に基づいた生産の流れを作り出し、不要な在庫の発生を防ぐ。
見える化
・目的: 問題点や改善の機会を明らかにし、関係者全員が状況を共有できるようにする。
・詳細: 生産状況、在庫量、不良発生状況などを視覚的に表示することで、問題の早期発見と対策を促す。
コメント